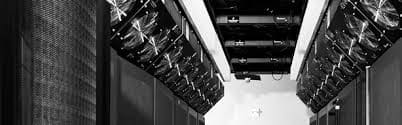
With equipment and applications that carry significant importance, it is highly recommended to find designers and contractors who have prior installation experience with Liebert High Density XD™ system within a data center environment. The XD™ system is just one component of the entire data center environmental support system and proper integration into the overall room design such as containment, fire protection interface, emergency generator backup and placement of XD™ air handlers for maximum efficiency is required. Properly installed and maintained, this system provides a reliable high density cooling capability with a small footprint and high energy efficiency.
High Density Cooling Application Tips
High capacity data center cooling systems are now required in many cases where there is inadequate space for conventional floor mounted perimeter cooling units. Computer rack loading advancing into the 20-30 kw per rack is a new challenge to provide adequate cooling. The Liebert High Density XD™ has a family of data center distribution air handlers that are compact and use a very small amount of aisle rack space or are ceiling hung using no floor rack space.
Energy Efficiency
The XDC160™ system has a total cooling capacity of 160 kwSensible (kwS). Sensible cooling is the type of heat that can be felt or measured by a thermometer and is not associated with humidity control. There are little or no personnel inside the sealed data center enclosure so heat removal is mainly computer output sensible heat. The XD™ system is designed to maximize this cooling requirement with air handlers that provide 100% sensible cooling. The XD™ system must be installed with perimeter Computer Room AC (CRAC) units providing humidity control and can be sized to provide secondary cooling and humidity control. Thus, the Liebert XD™ system becomes a highly efficient primary cooling system.
To compare the XD™ cooling capacity, the Liebert DS105™ perimeter 30-ton unit has a sensible capacity of 75 kwS. Two (2) DS105s will provide ~150 kwS cooling as compared with one (1) XD™ system rated at 160 kwS. The table below reflects total kVA power usage against comparable kWSensible cooling capacities.

1. Amperage values @ 480-3 phase
2. Amperage values are cooling only
3. Power usage for UX air handlers
4. Ration of sensible cooling over power usage. Higher value represents higher efficiency. Higher value represents more cooling per kVA power equaling a higher efficiency.
Design & Installation
As with any critical facility, proper planning and strategy for high density cooling is required. Liebert offers two types of heat rejection systems; 1) Use of building chilled water where the heat is rejected into a central building chilled water loop and, 2) Refrigerant based heat rejection either with air cooled remote condensers or a condenser water system utilizing an open tower or closed loop. Both system types utilize a pumped R134a refrigerant for heat removal from the critical space. There are three (3) refrigerant circuits on the XD™ system; two (2) for heat rejection with R407c refrigerant and a third circuit with pumped 134a refrigerant. The methodology for the pumped 134a refrigerant circuit is dissimilar to a typical refrigerant piping system. Thus, a full understanding of the 134a piping installation requirements are crucial. There is no water pumped for cooling means and since the coils are 100% sensible cooling, there is no need for condensate drains. Liebert’s design manual is very descriptive and detailed in how to plan and design the system. Liebert also has a helpful document titled, “Technical Note: Key Points of Design, Installation and Maintenance for Configuring Liebert XD™ Systems” that provides a brief technical overview of the system application.
The overall design application is to be integrated with the computer rack layout, hot or cold aisle containment and fire protection. Thus, the overall application is much more than just the equipment application. Fire protection with wet or pre-action sprinkler and clean agent will require smoke detectors and discharge nozzles within the contained aisle space. Many AHJs (Authorities Having Jurisdiction) will not allow the removal of water sprinklers even if the area is protected by clean agent. In this case, the primary fire protection is provided by the clean agent and the secondary protection is the sprinkler. The enclosure ceiling type selection becomes significant with how the smoke sensors and sprinkler/clean agent nozzles are installed and should be fully reviewed for adequate fire protection coverage.
Several incidental design considerations many times overlooked are:
- A minimum heat load must be discharged in the computer room for a single system or dual redundant systems to properly operate.
- Refrigerant piping design and methodology as described in the installation manual are necessary for capacity, oil return and overall reliability. It is always a good idea to prepare a piping diagram showing oil trap locations, double suction riser configuration and pipe sizes and have the Liebert factory engineers review and comment/approve.
- Contractor must flow a nitrogen bleed in the copper lines when brazing.
- When an A & B systems are installed, alternate the overhead or in-row fan coil units to provide coverage is one system fails or is out for maintenance.
- The in-row XDH™ unit has two independent coils and can be fed from both A & B XD™ units or from the same unit.
- The installation of additional pumped refrigerant ports will allow for expansion or the relocation of existing fan units to an area with excessive high temperatures.
- The room should be properly sealed to minimize perimeter area air infiltration. As a function of the room size, minimal conditioned air can be introduced into the room to provide positive pressure.
- The XD™ does not provide humidity control so additional Computer Room A/C (CRAC) units for humidity control are required.
Maintenance Service
The key to low maintenance is the thoroughness and quality of the initial installation. Many on-going maintenance issues are remnant from a poor installation. Such items as not using a nitrogen bleed when brazing, incorrect refrigerant piping sizing and methodology, piping pressure testing and overall system layout are to name a few. If the installation is not fully vetted by a qualified commissioning agent, then many of the installation inadequacies will cause on-going failures, unreliable system and high maintenance costs. In fact, many refrigerant compressor manufacturers attribute a large majority of returned warranty compressor failures are due to a poor installation. A properly installed system will be very efficient and highly reliable. If the system is fully vetted and commissioned, the on-going maintenance is rather simple. Standard maintenance procedures including checking the electrical connections, refrigerant charge, oil charge among other items are not that much different than a typical cooling system. Maintenance schedules shall also not impede necessary cooling in the critical space. The aforementioned Emerson manuals provide maintenance procedures for your use.
XD, XDH and other associated XD components are the registered trademarks of Emerson Network Power/Liebert.