Computer Room AC (CRAC) equipment operates continuously all year long regardless of outside temperature. Preventive maintenance (PM) is typically performed on a scheduled quarterly basis to check component condition and replace if necessary, to prevent pending failure. CRAC unit reliability and efficiency are essential for data center uptime.
Equipment PM reports and the information recorded become burdensome with multiple units and essentially unavailable at a moment’s notice. Imagine having a facility with 40 CRAC units and a unit is down at 3:30 am where the Field Specialist (FS) determines what prior issues the unit was experiencing will assist in determining a complete diagnosis including the root cause of a component failure. Correcting the root cause of any failure prevents the same failure occurring repeatedly and/or additional labor cost due to latent diagnosis.
The availability of the maintenance and corrective action work tickets are essential to fully determine equipment repair. This information can be immediately provided with electronic record keeping.
Each piece of equipment is identified with a QR/bar code located on the front panel of the equipment. The FS can scan the QR/bar code and on their tablet to access a PM sheet specifically drafted for the exact type of equipment. The PM sheet will be different for an air-cooled unit versus a chilled water unit and so on. The FS also has access to all the PM and repair records as far back to when the records were originally input.
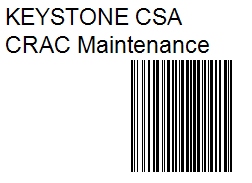
In addition to the prior records, the FE can access previous pictures of compromised or failed components. Below picture depicts deteriorating condenser fins. This observation can assist if the service call is based on compressor high head pressures. The client can also budget funding for a pending condenser replacement on a planned basis rather than an emergency if the condition is found early.
Equipment Operation & Maintenance manual, Technical Installation manual, electrical single lines, service bulletins and the names of the FS’s that performed any prior work are all instantly available. What a difference this makes in comparison to a handwritten service ticket description that may or may not be available or legible. The access to equipment information results in a faster diagnosis, quicker MTTR (Mean Time To Repair) and lower cost of ownership.
The electronic records assist the FS’s communication at a high level with office technical support and can hasten parts availability and/or schedule site delivery for immediate installation. Many repairs require a follow-up visit or task to complete the corrective action, i.e., changing a refrigerant suction filter and acid test on a compressor burnout replacement. The follow-up task can be performed and included in the work database.
The electronic work ticket and records ease of access provides an enhanced level of critical mission support. The electronic historical information, an experienced FS and office technical support will return the CRAC system back on-line in normal operating condition with an increased level of reliability and efficiency. The client can have a high level of confidence their technical service provider matches the advanced technology of their electronic environment.